When beginning the process of making wootz, one of the initial steps, besides creating a furnace, is determining the appropriate ingredients and quantities to use in the crucible. Some smiths find this to be a straightforward task, while others may encounter unexpected obstacles, leading to setbacks, frustration, and additional expenses. Although failures can be educational, it is preferable to begin with accurate information and experiment after achieving success. While many individuals seek a precise wootz steel recipe, it is not possible to provide one due to the significant variation in available ingredients for smiths worldwide. Instead, this guide will demonstrate how to identify the most suitable ingredients and calculate the necessary weights to develop a personalized recipe.
Carbon Source
To ensure reliable outcomes, it is advisable to begin with either the Co-fusion (carburizing the charge with white cast iron/sorel metal) or Carburization (carburizing the charge with graphite or charcoal) method. In the past, organic carbon sources like wood and bark were commonly used, but they can make it challenging for beginners to regulate the carbon content of their ingot. Once you have selected your carbon source, you must then select your iron source.
Iron Source
The type of iron used in the recipe can vary and include clean low carbon steel like 1018, electrolytic iron powder, sponge iron, pure iron flakes, or soft iron nails. The most important factor is that it is pure and has a known elemental composition. Using bloomery iron or unknown cast iron can be risky since their carbon content is unknown, and using them increases the chances of ingot failure. It’s crucial to ensure that any cast iron used is white cast iron and not grey cast iron to avoid the formation of graphite in the final ingot, which would result in poor or unforgeable steel.
Carbide Forming Elements
After determining your carbon and iron sources, it’s important to check if your iron contains too much manganese. If it does, then you’ll need to add higher levels of Carbide Forming Elements (CFEs) to offset it, while if it has no CFEs, you only need to add a small amount. If the manganese in your ingot is less than 0.3% of the weight of the metal, it won’t affect the wootz ingot’s quality. However, if it’s at 0.9%, it will affect the pattern in your final steel and require higher levels of CFEs. But adding more CFEs will make the ingot harder to forge and have a more dendritic or raw structure. There are several CFEs that can create patterning in your ingot, such as Vanadium, Niobium, Chromium, Molybdenum, Titanium, and Tungsten, each giving slightly different-looking carbide formations. Using pure metal crystals or powder is ideal for adding these elements, but if you don’t have access to them, you can use a piece of stainless steel with a known amount of Molybdenum and Chromium or tungsten carbide or vanadium carbide. It’s essential to remember that using small amounts of CFEs is preferable, around 0.01% or even less, unless you need to counter high manganese content. Manganese is good for steel’s hardening ability, but unless you’re using 100% pure iron, you’ll likely have sufficient manganese and trace CFEs. However, if your ingot is very pure with low CFE levels, you may encounter graphite formation problems during forging, especially if there’s significant silica in your steel or if it’s picked up from the crucible.
Final Carbon Content
The final decision to make is regarding the amount of carbon you want in your mixture. If you use a clay graphite crucible, a small amount of carbon will mix with the melt, which is acceptable. To prevent loss of carbon during the melting process, it is advisable to cover the crucible with a lid. The most commonly used carbon content for wootz ingots ranges from 1.3%C to 1.8%C. The higher the carbon content, the more challenging it is to forge and obtain a watered pattern. However, high-carbon content ingots have more carbides, resulting in a more prominent pattern, albeit with a rawer appearance. Beginners are recommended to use a carbon content of 1.5%C or less to increase their chances of success. It is recommended to roast the ingot at around 1100°C for a few hours to make it easier to forge, regardless of the mixture. To determine the amount of each ingredient required for the crucible, use our ingredient calculator after deciding on the carbon content and ingredients.
Wootz Calculator
Charging The Crucible
Once you have measured everything, you should put it into the crucible. It’s recommended that you layer you carbon source with your iron source, alternating between the two within the first 1/3 of your crucible. If you are using the carburization method, do not place graphite or charcoal at the very bottom or top of the crucible (See infographic below). This will help ensure that all of the carbon is utilized and prevent incomplete melting. Additionally, you should cut any iron into small pieces to promote even and rapid melting and clean it of rust to avoid porosity in the ingot. Load the crucible with your charge and add enough crushed glass to create a slag layer that is no more than 1-2cm thick after melting. This layer of glass will seal out the air, allowing for clean melting of the charge. In addition to sealing out the air, it also separates the molten charge from the atmosphere so carbon in the charge does not burn out. However, if the layer is too thick, there is a risk of cracking the crucible when removing the ingot. If you choose to seal your crucible, now is the time to do so using a thin layer of clay. If you are not sure what to use for a lid, the bottom portion of old, deteriorated crucibles work quite well.
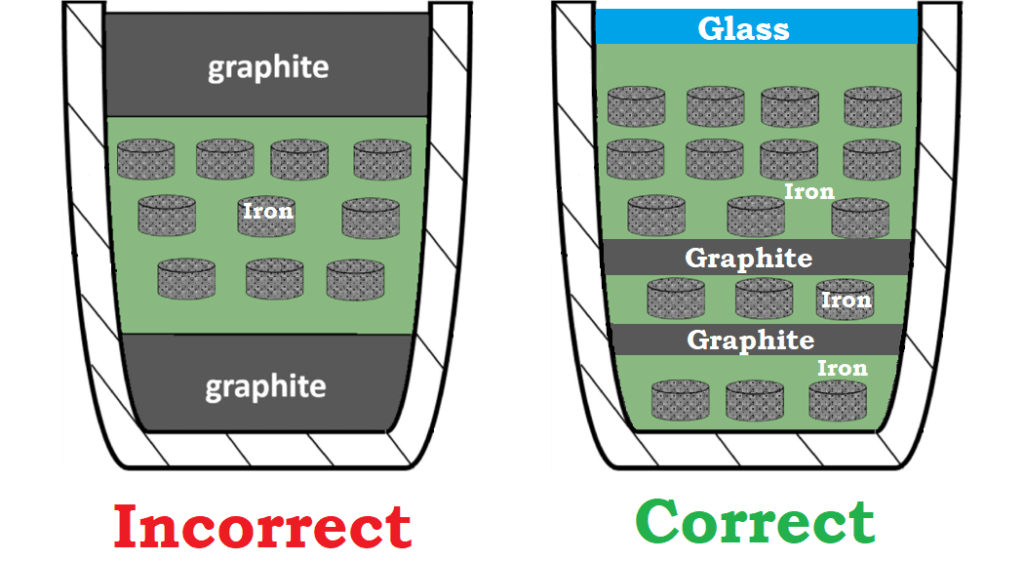
You are now ready to begin your first melt!
Firing Temperature
To determine the appropriate temperature to heat the crucible, refer to the Iron Carbon Phase Diagram to find the melting temperature for your desired carbon percentage in the ingot. The upper line on the diagram indicates the melting temperature. If using a co-fusion process charge, heat the crucible to at least 50°C above the listed temperature on the diagram. If using a carburization process, heat the crucible to a final temperature of 100°C above your desired temperature to fully melt the charge. It is important not to exceed 1600°C, as this can cause a carbon boil that consumes carbon and introduces silicon from the crucible walls. Allow the charge to sit at temperature for 30 minutes to ensure a good melt and let any gas escape. Then turn off the furnace, cover any holes, remove the burner, and allow the ingot to solidify and cool. Once safe to handle, carefully remove the lid and chip away any slag on top of the ingot that is no more than 1cm thick. With these steps, you can successfully begin the process of making wootz steel.
Ingot Failures From Improper Charging
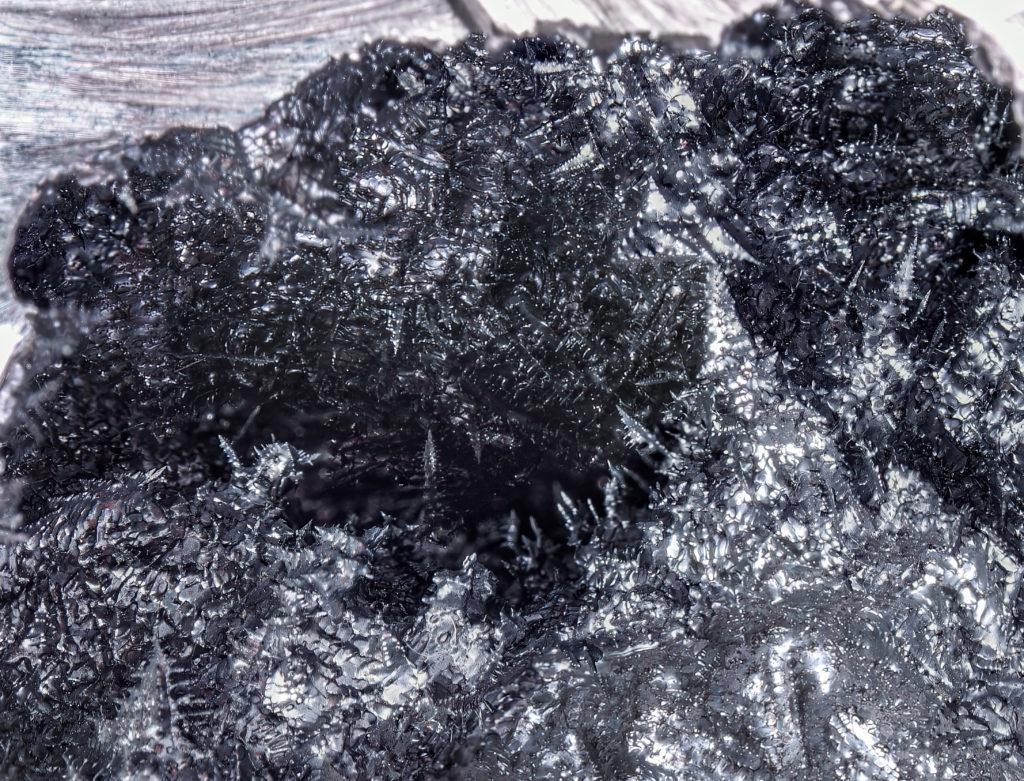
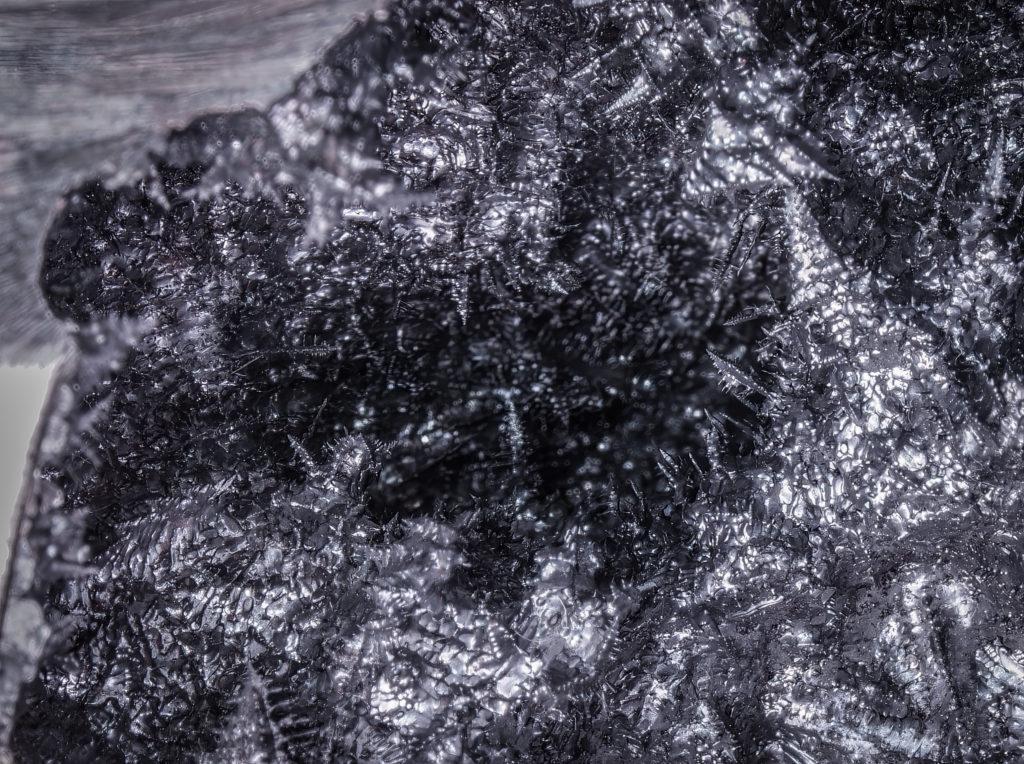